Actuators: A Comprehensive Guide On The Valve Operators


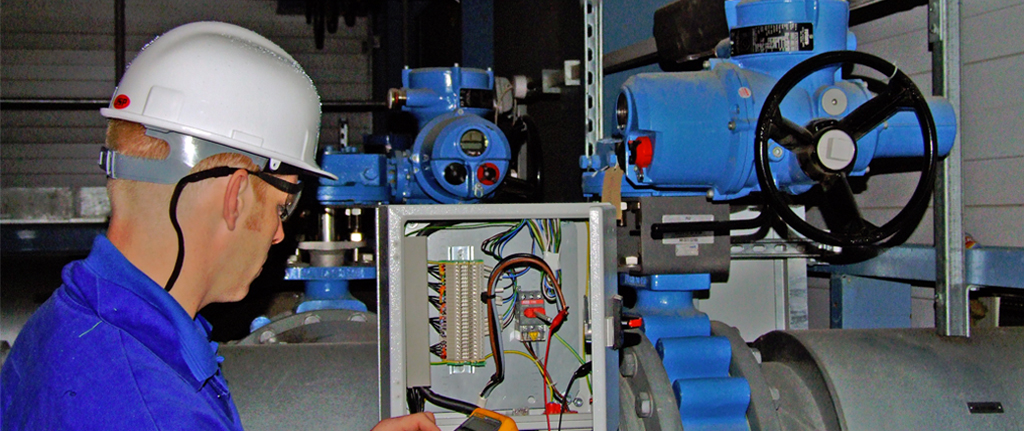
Needless to say, valves form the lifelines of a range of industries and systems. A ‘valve’ is a device that is used to control the flow of liquid in a process or machine. Manual valves often require some human attention in order to operate properly. This is done with the help of a geared mechanism attached to the valve. Undoubtedly, this human dependence makes it quite a long and strenuous process. This is where a valve actuator comes into the picture. As a valve is important for the proper functioning of a plant, a valve actuator is important for the proper functioning of a valve.
A ‘valve actuator’ is a device used for opening and closing a valve. How does it help? Firstly, valves can be operated from a remote location and secondly, large valves can be controlled easily and swiftly.
In this article, we will be talking in-depth about various types of valve actuators, their working principle along with their advantages and disadvantages.
Types of valve actuators
Valve actuators come in three different variants. These include pneumatic actuators, hydraulic actuators, and electrical actuators. Let us look into each of these types in detail.
a) Pneumatic actuators for Valves
As the name suggests, pneumatic actuators are used to control the position of the valve based on the air pressure. It adjusts itself to move with the changing air pressure valves, and thus controls the motion of the valves. This is the most common type of actuator used.
Pneumatic Actuators Working Principle
The idea behind their mechanism is simple. These actuators work by converting energy, mostly in the form of compressed air, into motion. This air is used to generate the energy required to adjust the movements of the valve. These can be of two types: Piston style and Diaphragm style. In the first case, the air acts strongly on the piston and this produces the necessary linear force. In the latter situation, a rubber diaphragm takes the force of the compressed air to bring in the required motion.
Advantages of Pneumatic Actuators:
- These actuators are designed in such a way that they are quick to respond and swift in motion.
- They have a higher actuation speed.
- When a valve is being open and closed frequently, pneumatic actuators are the best option.
- It does not require any explosion-proof measures before use.
- By altering the supplied air pressure, the output power can be changed according to the requirements
- These actuators require air to operate which is easily available and can be harnessed effortlessly.
Disadvantages of Pneumatic Actuators:
- High-pressure environments are not suitable for pneumatic actuators since this might compress the air.
- It is an expensive option since the air producing device has to be installed separately.
- Working with high-pressure air means there are chances of leakage.
b) Hydraulic actuators for Valves
Unlike the pneumatic actuators, hydraulic actuators make use of liquids in order to generate mechanical energy. The actuator, in general, comes with certain mechanical components. The liquid is used for creating pressure over these components in order to control the valves. They can create huge amounts of pressure.
Hydraulic Actuators Working Principle
Hydraulic actuators work mainly with the help of a fluid motor that is responsible for creating all the pressure required. Hydraulic power is used to bring about this motion. The output received can be categorized along the lines of linear, rotatory or oscillatory. The main benefit derived from the arrangement is huge volumes of power since liquids are almost impossible to compress. The system consists of a long cylindrical tube along which slides a piston which can move only in one direction.
Advantages of hydraulic actuators:
- Hydraulic actuators are perfect for systems requiring a huge amount of force. As compared to pneumatic actuators for valves, these can produce 25x power.
- Since liquids are almost incompressible, the arrangement will be able to hold the torque in its position without any additional external supply.
- Even if the pumps are kept far away from the hydraulic actuators, they can work well with the efficiency.
Disadvantages of hydraulic actuators:
- The liquid can get leaked. As a result of this, there is a potential loss of efficiency that could affect its performance.
- The working of the system might get a little messy and can have cleanliness issues.
- There are quite a few components required to assemble this system like a fluid reservoir, heat exchanges, and the likes. These take up too much space and also make the arrangement more expensive.
c) Electrical actuators for Valves
As the name suggests, electrical actuators work on electricity and require a strong power source. The main idea is to convert electrical energy into mechanical energy. These actuators are generally suitable for valves which make multiple turns.
Electrical Actuators Working Principle
An electrical actuator essentially works on a motor that converts electrical energy to mechanical torque. By its motion, it will be able to control the movement of the valves, by initiating motion as well as preventing it. Electric actuators are accompanied by a complex circuit design.
Advantages of Electric Actuators:
- Electrical actuators work with the maximum accuracy in terms of the force generated.
- In the case of faulty situations, electric actuators can be fixed immediately, all thanks to the easy reprogramming solutions. It requires less maintenance and can produce good results.
- They can help you to easily control torque, velocity or force. Electric actuators are easiest to handle, better than the pneumatic actuators for valves.
- The electric actuators operate noise-free, making it a comfortable arrangement to work with.
- With the absence of any kind of fluids for its operation, electric actuators eliminate the risks of leaks and thus are safe for the environment.
Disadvantages of Electric Actuators:
- The failure rate of an electric actuator is much higher than that of a pneumatic actuator. Further, it is time-consuming as well.
- The initial setup cost of such an actuator is high and can disturb your finances if you are on a tight budget.
- Since it is running on a motor, it is more prone to wear and tear and has a low durability.
Wrapping Up
It is imperative to note the importance of valve actuators. Regardless of the type of valve actuator used, they help in controlling the system and deal with the flow changes.
What are your views on this? How do you ensure that your valves are functioning properly? For more information about various valves specifically required for your industrial plants / business, Contact Flowspec and we will be happy to answer your questions and give you all the details you need.