Butterfly Valve: An In-Depth Mechanism You Need To Know


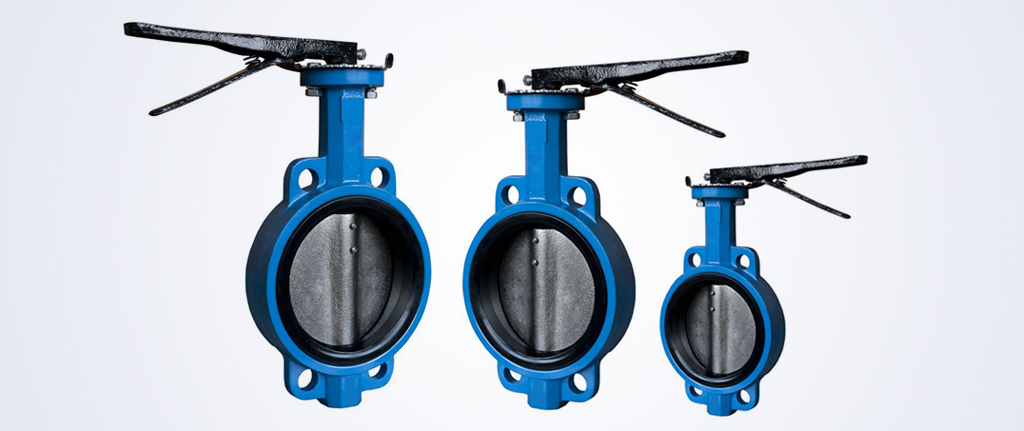
The butterfly valve is a type of one fourth-turn rotary motion valve which is used as a throttling valve to control and regulate the flow through a system. Butterfly valve has its own set of advantages which include good control capabilities, quarter-turn, and openness for diminished plugging systems. Further, the capability of butterfly valves to work in areas with limited space and deliver a high coefficient of flow makes them an important part of industries today.
However, since it is difficult to clean their internal parts, they are not recommended to be used in industries like medical and food processing applications where sterility is an important factor.
Control methods of butterfly valves
Butterfly valves function by controlling the flow of the liquid that passes through them depending on the method of control. A butterfly valve consists of a metal circular disk, also called vane. This disc pivots at a right angle to the axis of the direction of flow in the pipe.
When the valve is rotated, the circular disc seals itself against the valve seats. The disc then allows the flow to pass through by offering it a low resistance.
Butterfly valves operate faster as they are required to be rotated a quarter turn in order to close or open a passageway.
Media
Media is a characteristic term which is used to describe the system material. Media plays an important role in deciding the type of material which should be used for the construction of the disc
Media that pass through the valve system includes:
- Solids
Various factors should be kept into consideration while customizing a valve for an abrasive and semi- abrasive material operation. A disc which will close on dry bulk materials is more likely to get premature wear and tear on the rubber seats and also obstruct the orifice created by the disc. This further may lead to the bridging of the materials on the valves inlet side.
Further, it may even lead to the jamming of the dry materials or the disc getting jammed and getting trapped between the disc and seat which further may cause a serious line of inefficiencies and in turn, delay its working and effectiveness.
- Gas
When dealing with gasses, it is highly recommended that the valve seals should be tight and as per the systems functioning and the specified leakage rate at the given pressure and temperature. If the volume is small, the usage of its equal percent characteristics is recommended.For huge volumes, the linear characteristics are preferred if the system pressure fall is attainable to the valve at more than 25%.
- Liquid
The systems seals need to be tight to avoid damage and leakage. If the calculation is greater than 25% of the pressure drop, it is highly recommended to follow a linear characteristic. If it is less than the given percentage, then the fall in drop at its utmost flow conditions can be calculated through the parallel percentage characteristic.
Butterfly valve components
The body motion and construction of a butterfly valve is unique when compared to other valves.
- Body construction
Butterfly valves have 2 types of body types. These include lug and wafer type namely.
The lug shape has protruding legs. The metal inserts are installed in the bolt’s hole. The installation is done between 2 flanges by using separate bolts for each flange. The advantage of this body is that it makes a way for dead-end service.
The other body type, wafer, is developed between the flanges with the help of bolts, studs, and nuts. It doesn’t have protruding legs and is easy to install or replace. It is cheaper too. A drawback with this is that some valves with this body do not cast a decent seal and therefore demand extra care.
- Valve seat
Most of the butterfly valves use disc seals and elastomeric seals. When the disc seals adjacent to the diameter of its body, it stops the flow. The seals may be pressed, locked in or bonded to its body. Some seals used clamp rings or backing loop to enclose extrusion of the O- ring. In some designs which are meant for high and durable performances, the seals are implemented by an interference- fit design, which is created by the pressure in the pipelines, thereby, increasing its interference amidst the seat and its disc.
- Valve disc
Butterfly valves have separate disc and stem which are fastened in sync. The stem might be fused with bolts or the disc might be allowed to float and locate its center in the seat. The center here is shaped when the bore of the upper stem fits into a hex/ square shaped stem. This method is used for corrosive applications as the covered discs are used by eliminating the external fasteners.
Performance specifications
There are various terms associated with butterfly valves that denote their performance during an operation. Some of these include:
- Wetted and non-wetted
Wetted valves are the ones which have their body and stem exposed to the media. On the other hand, non-wetted valves are those which keep their body and stem in isolation from the system media.
- Liner and equal percentage flow
In a linear flow, the flow rate is in proportion to the amount the disc travels. For example, if the disc is 45% open, the flow rate would be 45% of the maximum flow. On the other hand, an equal percentage flow is a flow in which the flow rate is in proportion to the change in valve opening.
- Pressure drop
Pressure drop is the difference between the pressure between the outlet and inlet valve. It plays an important role in determining the size of the valve required.
Butterfly valves applications
Butterfly valves are widely used in numerous processes and applications as they are compatible with different media types which include corrosive materials, waste treatment, slurries and water systems. Some of their uses include:
- High temperature and pressure steam and water dispensation.
- Vacuum service.
- Slurries and any other similar service.
- Fire protection, gasses, air and cooling water.
Wrapping Up
All butterfly valves are configured differently in terms of shape, sizes, installations and fittings. These valves are also used in automobile systems and the best example is the carburetor of a car. Here, the valve is used to control the air- flow to the car’s engine. It is meant to open partially to regulate the amount of air passing through. For more information about various valves specifically required for your industrial plants / business, Contact Flowspec and we will be happy to answer your questions and give you all the details you need.