Common Mistakes When Installing Inline Duckbill Check Valve


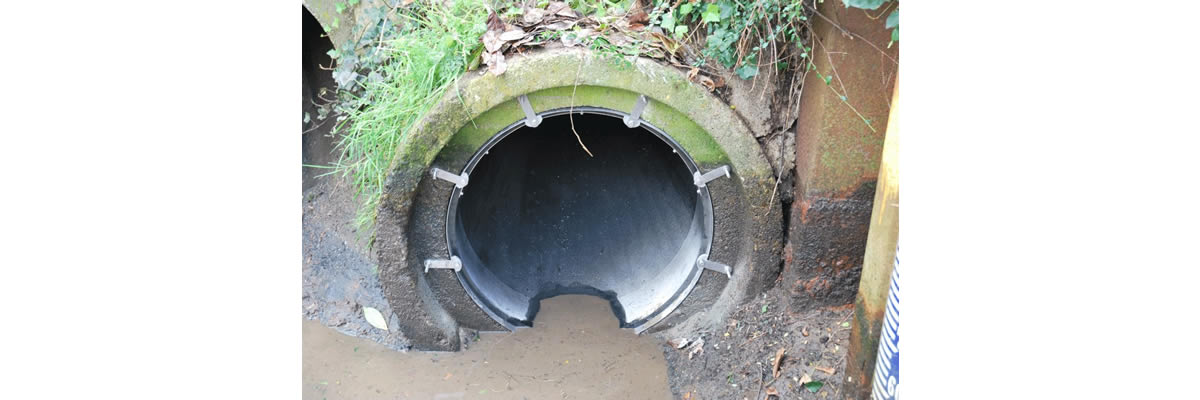
Inline duckbill check valve utilizes slow-closing technology, and this means that the wide circular end will not open until the inlet pressure acting upon it is greater than the outlet pressure. It must be said that the inline duckbill check valve will only release water in one direction, as the wider end will open to receive fluids, pushing them out through the duckbill to their next destination.
The duckbill is unable to open and remains closed despite the pressure exerted upon it. This means that water cannot move in two directions; it can only move forward. That said, it will be necessary to properly install the inline duckbill check valve and avoid these common mistakes.
Using the Incorrect Sizing
It is a common misconception that the inline duckbill check valve must be sized to the line. This is incorrect, because the wide circular opening of the inline duckbill check valve will have a lip whose diameter is greater than the pipe. This ensures that the valve will stay tightly in place without moving or becoming dislodged.
Attempts to size the inline duckbill check valve to the line could result in an inability to install the piece, or it could enable the valve to allow backflow to occur, as it won’t be properly sealed if it is too big. The correct installation method is to size the inline duckbill check valve for the application so that everything will fit together tightly.
Installing Them Like On/Off Valves
It is vital that you understand what your needs are when choosing a valve. Sometimes, inline duckbill check valves will be confused with on/off valves, and this is a valve that can shut off or completely open when specific conditions have been met.
These do not serve the purpose of preventing backflow, and they do not serve any regulatory purposes either. The inline duckbill check valve will, however, work according to the pressures enacted upon it and needs to be installed accordingly.
Subjecting Them To The Wrong Conditions
The inline duckbill check valve will respond to its environment, as it is flow sensitive. The valve will always be in the path of running water, and when there is not enough of this flow, it can cause movement inside the valve. This can cause wear to occur, as parts can experience rubbing.
It is essential to accurately assess the anticipated flow and to correctly calculate the size of the line that will be needed to transport that water to prevent problems from occurring. Neglecting this step can cause a breakdown in the materials and failure of the component. Though this process may take time, the eventual result could be the allowance of backflow into the feeding stream.
It is vital to also understand the pressure drop, and this is defined as the difference between the pressure exerted on the open and duckbill portions of the inline duckbill check valve. A pressure drop occurs when flow resistance is present, acting as a frictional force on the fluid.
These frictional forces, in turn, can cause the calculated flow to drop. In addition, it is vital to take the position of the valve into account when estimating these numbers. A valve that is fully open will create a different pressure drop than one that is only partially open. Other valves may not require technicians to take these numbers into consideration, as their construction and functionality is widely divergent from the inline duckbill check valve.
Flowspec-Luokai is a fine purveyor of inline duckbill check valves suited for industrial purposes and designed for a variety of uses, including sewage treatment plants, storm drain management, highway and airport water removal, and more. Contact us if you have questions, and we will be happy to answer them.