Globe Valve: A Comprehensive Study


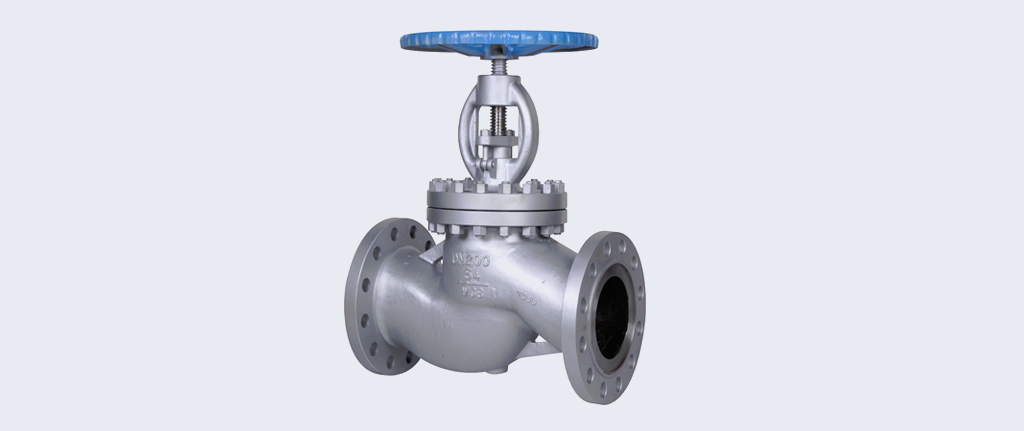
A globe valve is a kind of linear motion valve. It is used to start, stop and regulate flow with the help of a disk which can completely close or open the flow path. Globe valves have a higher pressure drop when compared to other valves and hence, they are widely used for isolation and throttling services. They are usually used in cases where the pressure drop through the valve is not a controlling aspect. The size limit of the valve is NPS 12 (DN 300), as the system pressure applied on the disc is ultimately transferred to the valve stem.
With that being said, let’s now understand how globe valves work.
Mechanism of globe valves
Globe valve mechanism is pretty easy to understand. Generally, globe valves are used to control the flow. Various aspects like pressure drop, the range of flow control and duty are considered while designing a valve in order to extract the maximum output from it. Valves that experience high-differential pressure throttling service need specially designed valve trim. The maximum differential pressure exerted on the disc should not exceed 200psi or 20% of the maximum upstream pressure, whichever is less. For those exceeding this differential pressure, special trim valves can be used.
Body designs of globe valves
There are three body designs for globe valves. They are:
- TEE Pattern globe valve design
This design has a Z-shaped diaphragm and is the most common body design for globe valves. The seat has a horizontal setting which permits the disk and stem to move perpendicular to the horizontal line. Tee pattern design has higher pressure drop and the lowest coefficient of flow. It finds its use in severe throttling services like bypass lines around a control valve. This type of globe valve is used where throttling is necessary and pressure drop is not a concern.
- Angle Pattern globe valve design
This globe valve design is a modification of the Tee pattern globe valve. In this design, the ends of the valve are at 90 degrees to each other and fluid flows with a single 90 degrees turn. The coefficient of flow is slightly lower than the wye pattern valves. Angle pattern globe valves are used in cases that have periods of pulsating flow due to their capability to handle the slugging effect of this kind of flow.
- Wye Pattern globe valve design
This valve is an alternative for the high-pressure drop seen in globe valves. The stem and seat are at an angle of 45 degrees which offers the least resistance to flow and gives a straight flow path at full opening. They can be kept open for a long time without severe erosion. They are used for throttling during startup or seasonal operations. When they are used in drain lines that usually remain closed, they can be rod through to remove debris.
Components of globe valves
- Disk
Disk, ball disk, and plug disk are the most common disk designs. Composition disk ensures a tighter closure using a non-metallic insert ring. Ball disk is used in systems that have low pressure and low temperature. It is used to stop and start the flow. Plug disk offers better throttling than the above variants. It is available in several designs.
- Seat
Seats of the globe valves are either screwed or integrated into the valve body. Most valves have backseats inside the bonnet which provides a seal between bonnet and the stem.
- Stem
There are two methods of connecting the disk and the stem in globe valves. First is the T-slot design in which the disk slides over the stem. The second is the disk nut design in which the disk is screwed into the stem.
Construction of a globe valve
Globe valves are usually characterized by rising stems and the ones with larger sizes have the outside-screw-and-yoke construction. They have components same as that of gate valves. They have seats in a plane which is either inclined or parallel to the line of flow.
Globe valves are easy to maintain as the seats and discs can be easily renewed or replaced. As a result, they are used for services which necessitate frequent valve maintenance. If the valves are adjusted often, it is better to have shorter disc travel so as to save operation time. This is especially true if the valves are operated manually.
The globe valve specification varies as per the type of disc used. Discs that are plug-type have tapered long configuration with a wide bearing surface. Such a seat offers maximum resistance to the fluid stream’s erosive action. The composition disc has a flat face which is pressed against the seat opening like a cap. Such an arrangement is not appropriate for high differential pressure throttling.
Cast-iron globe valves have seat rings and disc made of bronze. For temperatures up to 399 degree Celsius, the steel globe valves have the trim made of stainless steel which provides resistance to galling and seizing. Differential hardness values are obtained when mating faces are heat-treated.
When the valve is closed, the seating surface is ground to enable full-bearing surface contact. Alignment is maintained by a long disc locknut for lower pressure classes. But in the case of higher pressures, disc guides are casted into the valve body. The disc turns on the stem freely to stop galling of the seat ring and disc face. To prevent the galling of the disc and stem at the point of contact, the stem bears against a hardened thrust plate.
Globe valves find wide industrial usage, all thanks to a number of advantages that they offer.
Advantages of globe valves
- Moderate to good throttling capability
- Easy to resurface or machine the seats
- Good shut off capability
- Available in wye, tee and angle patterns each having unique capabilities
- Shorter stroke when compared to a gate valve
- When the disk is not attached to the stem, the globe valve can be used as a stop-check valve
Disadvantages of globe valves
- Globe valve function requires a larger actuator or a greater force to seat the valve (with pressure under the seat)
- Higher pressure drop when compared to a gate valve
- Shutoff flow over the seat and throttling flow under the seat
Due to their advantages, globe valves are widely used in a number of applications.
Applications of globe valves
The applications of globe valve include the following:
- Turbine seals and drains
- Chemical feed, feed water, extraction drain systems and condenser air extraction
- Cooling water systems where the flow has to be regulated
- Turbine lube oil system
- Fuel oil system where the flow is regulated and leak tightness is important
- Low point drains and high-point vents when safety and leak tightness are important concerns
- Main steam vents and drains, boiler vents and drains and heater drains
Conclusion
The good shut off capability and the throttling capacity have made globe valves suitable for a range of industries. What are your views on this? How do you ensure that your valves are functioning properly? For more information about various valves specifically required for your industrial plants / business, Contact Flowspec and we will be happy to answer your questions and give you all the details you need.